Exploring Autodesk Fluid Dynamics: An In-Depth Analysis
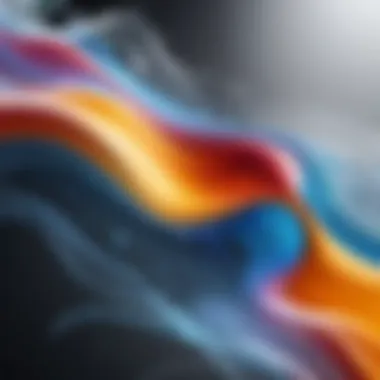
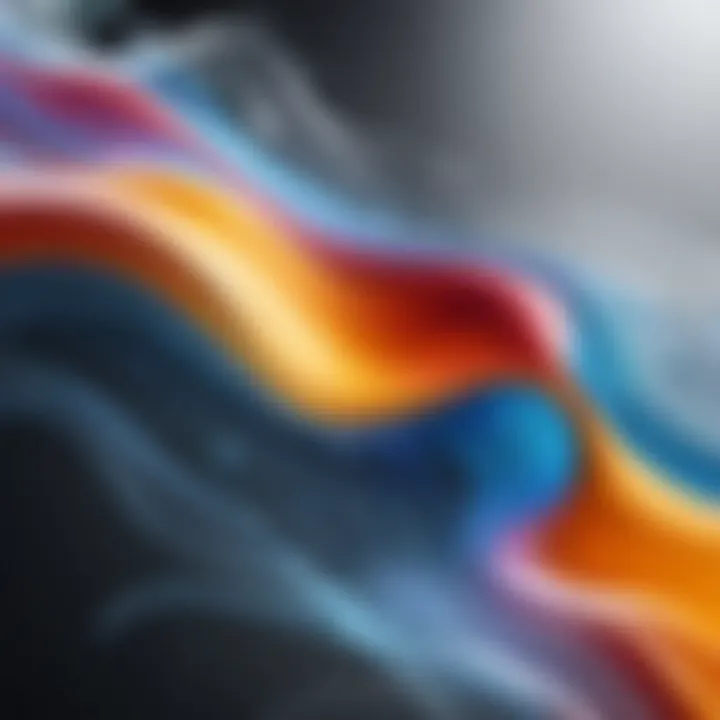
Intro
Fluid dynamics is a crucial field in various engineering applications. Autodesk has developed robust software solutions that simplify the complexities involved in fluid simulations. Understanding how these tools function can empower engineers and researchers. This article provides a deep look into Autodesk Fluid Dynamics, discussing various methodologies, applications, and benefits.
Software Overview
Purpose and function of the software
Autodesk Fluid Dynamics software is designed to simulate the behavior of fluids under various conditions. The primary purpose is to create accurate representations of how fluids interact with their environments. This capability is vital for industries such as aerospace, automotive, and civil engineering. By providing tools to analyze fluid flow, engineers can make informed decisions during the design process.
Key features and benefits
The software integrates several powerful features that enhance its usability:
- Advanced Simulation Engine: Utilizes computational fluid dynamics (CFD) to deliver precise fluid behavior results.
- User-Friendly Interface: Designed for ease of use, allowing users to focus on simulations rather than software mechanics.
- Extensive Material Library: Offers a variety of fluids and materials, enabling more realistic simulations.
- Visualization Tools: Facilitates the interpretation of simulation data through graphs and 3D models.
These features contribute significantly to improving design processes, reducing costs, and optimizing product performance.
Installation and Setup
System requirements
Before installing Autodesk Fluid Dynamics, ensure that your system meets the following requirements:
- Operating System: Windows 10 or later
- RAM: Minimum 16 GB (32 GB recommended for large simulations)
- Disk Space: At least 10 GB of free space
- Graphics Card: DirectX 12 compatible with a minimum of 4 GB memory
Installation process
Installing Autodesk Fluid Dynamics is a straightforward process. Follow these steps:
- Download the installer from the Autodesk website.
- Run the installer and follow the on-screen instructions.
- Enter your Autodesk account information when prompted.
- Select the installation type (default or custom).
- Complete the installation and restart your computer if necessary.
After installation, the software will be ready for use, providing access to its powerful features for fluid dynamics analysis.
Foreword to Fluid Dynamics in Autodesk
Understanding fluid dynamics is essential for various disciplines in engineering and technology. Autodesk plays a significant role in enhancing the methods, processes, and results associated with fluid simulation. This section will cover fundamental aspects of fluid dynamics and the contributions made by Autodesk to this domain. The significance of Autodesk's tools cannot be understated, as they provide a framework for better design choices and the analysis of complex fluid behaviors.
Defining Fluid Dynamics
Fluid dynamics is the study of how fluids move and the forces that affect them. This field merges principles from physics and engineering to understand and predict fluid behavior under different conditions. In both natural and artificial systems, fluids exhibit complex movements influenced by factors such as pressure, temperature, and viscosity.
Fluids can be classified as incompressible and compressible. Incompressible fluids maintain a relatively constant density, while compressible fluids see variations in density under pressure changes. Applications of fluid dynamics span numerous sectors, including aerospace, automotive, environmental science, and civil engineering. Mastering fluid dynamics allows professionals to innovate and create solutions that are more efficient and effective.
The Role of Autodesk in Fluid Dynamics
Autodesk has established itself as a leader in 3D design, engineering, and entertainment software. Its approach to fluid dynamics combines comprehensive simulation capabilities with user-friendly interfaces. Autodesk's initiatives in this field provide valuable resources for engineers and designers, allowing them to conduct analyses that were previously time-consuming and complex.
Autodesk CFD (Computational Fluid Dynamics) serves as one of its flagship tools in this regard. It allows users to simulate fluid flow and analyze the behavior of cooling liquids, airflows, and other fluids. The software incorporates robust physical models, ensuring high accuracy in results. With Autodesk's innovations, professionals can visualize fluid behavior, validate design choices early in the process, and refine systems to meet specific criteria.
As industries increasingly prioritize efficiency and sustainability, the role of Autodesk's tools in fluid dynamics becomes even more prominent. Understanding these concepts and their applications is crucial for professionals aiming to excel in technical fields.
Core Concepts of Fluid Simulation
Fluid simulation serves as the backbone of visualizing complex fluid behavior in various fields. Understanding the core concepts is critical for anyone working with Autodesk Fluid Dynamics. There are several essential elements that provide a framework for how fluids behave and interact with their environment. This section will explore foundational ideas in fluid simulation, such as the Navier-Stokes equations, turbulence modeling techniques, and the importance of boundary conditions.
Navier-Stokes Equations Overview
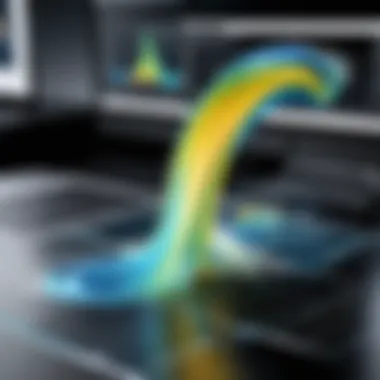
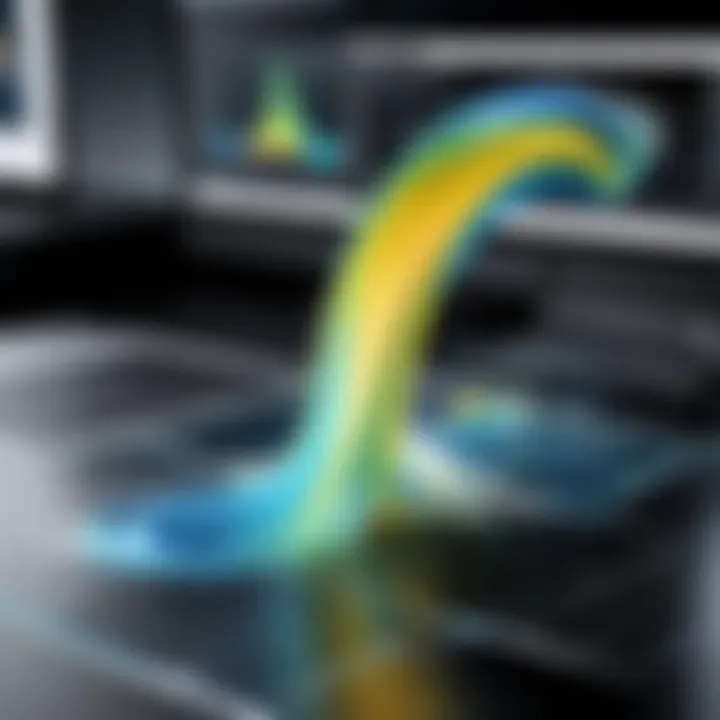
The Navier-Stokes equations are a set of nonlinear partial differential equations that describe how velocity, pressure, and density of a fluid evolve over time. These equations are pivotal in fluid dynamics as they account for various factors such as viscosity and external forces.
Fluid dynamics software like Autodesk CFD uses these equations to solve complex simulation problems. Understanding these equations enables engineers to predict fluid motion accurately. This predictive capability is vital in industries such as aerospace, where aerodynamic forces directly impact design efficiency. The equations can be complex, but their solutions can provide deep insights into fluid behaviors under different conditions.
Turbulence Modeling Techniques
Turbulence refers to irregular or chaotic flow patterns in fluids, which are difficult to predict. Modeling turbulence accurately is crucial for simulating real-world fluid dynamics effectively. Several techniques exist, each having unique advantages and disadvantages.
- Reynolds-Averaged Navier-Stokes (RANS): This method averages the effects of turbulence, simplifying the computation but may overlook some key phenomena.
- Large Eddy Simulation (LES): It simulates larger turbulent structures while modeling smaller ones, striking a balance between accuracy and computational efficiency.
- Direct Numerical Simulation (DNS): Uses fine mesh to resolve all scales of turbulence but is very resource-intensive and often not feasible for complex simulations.
The choice of turbulence modeling technique can significantly influence the outcome of a simulation, impacting both the design process and engineering calculations.
Boundary Conditions in Simulation
Boundary conditions define how fluid interacts with its environment within the simulation. They are critical for accurate results as they establish limits on the simulation's behavior. Several types of boundary conditions are commonly used:
- Inlet Conditions: Specify how fluid enters the domain, affecting flow patterns significantly.
- Outlet Conditions: Determine how fluid exits, impacting overall pressure and flow rates.
- Wall Conditions: Govern how fluid interacts with surfaces, affecting drag and resistance, which is particularly important in aerodynamics.
Choosing appropriate boundary conditions is essential for achieving valid simulation results. Misestimation in boundary settings can lead to incorrect predictions, undermining the design's integrity.
Understanding these core concepts equips software developers and engineers to leverage Autodesk Fluid Dynamics effectively. Proper application of the Navier-Stokes equations, turbulence modeling, and boundary conditions ultimately enhances the reliability and relevance of fluid simulations.
Autodesk Fluid Dynamics Software Solutions
Autodesk's fluid dynamics software solutions play a pivotal role in modern engineering and design, making complex simulations accessible and practical for users across various industries. These tools enable the analysis of fluid flows, heat transfer, and other dynamic processes critical to product design and performance.
Among Autodesk's offerings, Autodesk CFD stands out as a comprehensive tool that harnesses advanced computational fluid dynamics to meet the needs of engineers and designers. The advantages of using such software extend beyond mere simulation; they offer insights that directly influence the end productโs effectiveness and efficiency.
Autodesk CFD
Autodesk CFD provides essential capabilities that facilitate fluid flow and thermal simulation. It empowers engineers to visualize complex interactions in their designs without the need for extensive physical prototyping. This allows for reduced project timelines and cost savings, as potential design flaws can be identified early in the development process.
With features that accommodate a range of applications, Autodesk CFD is suitable for industries, including aerospace, automotive, and renewable energy, allowing each sector to tailor simulations according to their requirements.
Features of Autodesk CFD
User-Friendly Interface
The user-friendly interface of Autodesk CFD is a significant factor in its broad adoption among professionals. It streamlines simulation tasks and allows users to focus on the analysis. Users often cite how easy the tool is to navigate, encouraging faster learning curves and increased productivity.
A noteworthy characteristic is the intuitive layout, which minimizes the time required to set up and execute simulations. This ease of use contributes to its popularity among newcomers and seasoned professionals alike. While it simplifies many complex processes, users should still have a basic understanding of fluid dynamics principles to maximize its capabilities.
Robust Simulation Capabilities
In terms of simulation capabilities, Autodesk CFD offers robust tools for analyzing various fluid behaviors under different conditions. This capability stands as a core strength of the software, allowing for detailed analysis of turbulent, laminar, and multiphase flows.
The key characteristic of these robust capabilities is the ability to simulate real-world conditions accurately. Engineers can assess how their designs will perform in scenarios ranging from standard operations to extreme conditions. The trade-off, however, lies in the computational resources required, as more detailed simulations demand greater processing power and time.
Integration with Other Autodesk Tools
Another excellent feature of Autodesk CFD is its integration with other Autodesk tools, such as AutoCAD and Revit. This integration allows seamless data transfer, enabling users to incorporate fluid dynamics analyses into their broader design workflows.
Its compatibility enhances the overall efficiency of design projects, as users can work within an interconnected framework. This synergistic environment is beneficial for those already embedded within the Autodesk ecosystem. However, users must ensure that they maintain updated versions of interconnected software to avoid compatibility issues.
"The integration of Autodesk CFD with other tools allows for a holistic approach to product design, where fluid dynamics is just one aspect of a comprehensive analysis."
In summary, Autodesk Fluid Dynamics solutions cater to the complex needs of fluid dynamics analysis while promoting an engaging user experience. Their features not only enhance practical application but also bridge the gap between theory and real-world scenarios, making them invaluable tools in today's engineering landscape.
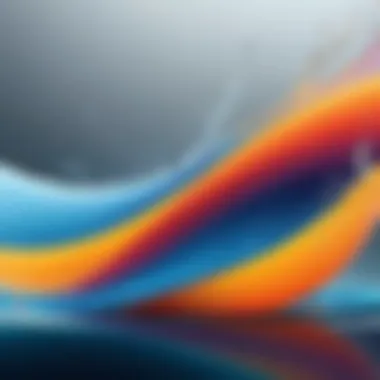
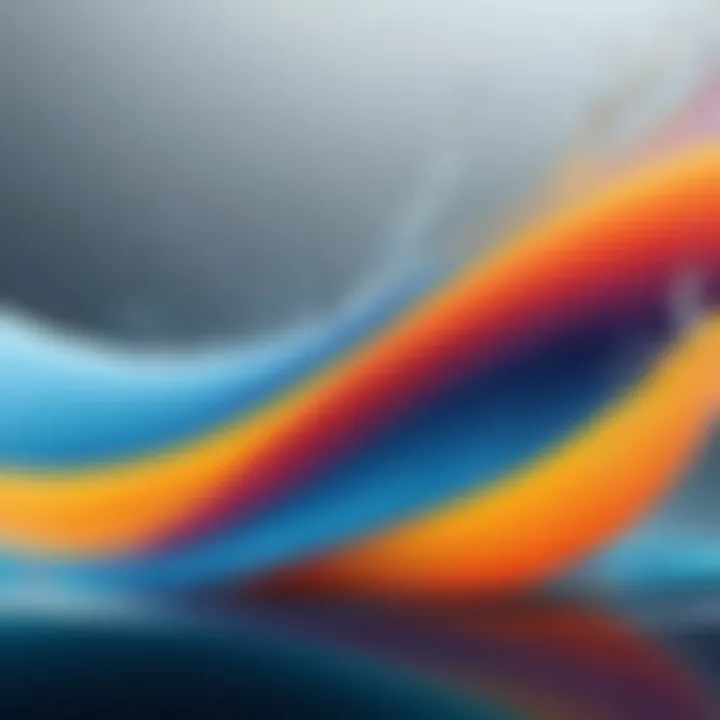
Practical Applications of Autodesk Fluid Dynamics
Understanding the practical applications of Autodesk Fluid Dynamics is crucial for comprehending how these technologies shape different industries. The real-world uses of fluid simulation extend far beyond academic interest; they have tangible impacts on engineering projects, aerospace designs, environmental solutions, and more. This section will explore these applications, emphasizing the effectiveness and significance of Autodesk's tools in various scenarios.
Engineering and Design
In the field of engineering, fluid dynamics plays a vital role. Engineers utilize Autodesk tools to simulate how fluids interact with their designs. This capability is essential when developing products that will face air or water flow in their lifecycle. For instance, when designing cooling systems for machinery or structures, engineers can visualize how fluids will behave, altering chances of overheating and mechanical failure.
Key benefits include:
- Enhanced Visualization: Engineers can see fluid behavior in a 3D space, offering insights that traditional methods cannot.
- Prototyping Efficiency: Autodesk fluid dynamics tools allow for faster iterations of designs, reducing the need for physical prototypes.
- Performance Optimization: With advanced modeling, engineers can refine their designs to improve performance significantly.
Aerospace and Automotive Industries
Both the aerospace and automotive industries heavily rely on fluid dynamics for successful design and functionality. In aerospace, understanding aerodynamics is essential for flight. Autodesk software aids in simulating airflow around fuselages and wings. Similarly, automotive engineers must consider how air flows over vehicles to enhance performance and fuel efficiency.
Specific applications include:
- Aerodynamic Testing: By assessing various shapes and materials, engineers can improve vehicle performance before physical production begins.
- Safety Enhancements: Simulations can help identify potential safety issues, enabling timely resolutions that protect both consumers and manufacturers.
- Regulatory Compliance: Fluid dynamics simulations assist companies in meeting industry regulations concerning emissions and safety.
Environmental and Energy Solutions
Fluid dynamics simulation has crucial implications in environmental science and energy efficiency. As global concerns rise around climate change and resource management, understanding fluid behavior becomes increasingly important. Autodesk tools provide insights into how fluids travel, mix, and react in various conditions.
Applications in this domain include:
- Water Resource Management: Simulations can forecast water flow in rivers and reservoirs, aiding in effective resource allocation and disaster preparedness.
- Renewable Energy: In wind turbine design, fluid dynamics is instrumental in maximizing energy capture by analyzing airflow patterns.
- Pollution Control: Software helps model pollutant dispersion in air and water, which is vital for assessing environmental impact and formulating response strategies.
Autodesk Fluid Dynamics tools not only enhance design processes but also play a crucial role in addressing global challenges through innovative engineering solutions.
Benefits of Using Autodesk Fluid Dynamics
Fluid dynamics simulations provide significant advantages across various domains. The utilization of Autodesk fluid dynamics tools can enhance operational effectiveness and lead to superior outcomes in design and analysis. Understanding the specific benefits is fundamental for professionals involved in engineering, software development, and academic research.
Enhanced Accuracy in Predictions
One of the foremost advantages of Autodesk fluid dynamics is the increased precision in predictions related to fluid behavior. When simulating fluids, engineers require accurate data to make informed decisions. Autodesk tools employ advanced algorithms and models honed through extensive research to provide realistic simulations.
With Autodesk CFD, users can expect enhanced reliability in simulation outputs. This accuracy directly translates to better performance in real-world applications, ensuring that designs are securely validated before physical testing or production emerges. The software's capabilities allow analysts to visualize flow patterns and optimize design features. This optimization process leads to less trial and error in prototyping phases and more confidence in final products.
Improved Design Efficiency
Efficiency in design processes is another significant benefit provided by Autodesk fluid dynamics systems. The software offers tools that enable faster iterations in the design phase compared to traditional methods. Being able to simulate different scenarios quickly helps engineers find optimal solutions effectively.
In many industries, especially in aerospace and automotive, the ability to test various design configurations rapidly allows for innovation. This accelerated design process supports rapid prototyping and reduces time-to-market for products. Improved efficiency can lead to significant competitive advantages, allowing companies to adapt to market demands swiftly.
Here are some aspects contributing to improved design efficiency:
- User-friendly interface simplifies navigation and increases productivity.
- Comprehensive support materials and community forums are available for troubleshooting.
- The integration of simulation results into overall project workflows streamlines project management.
Cost-Effectiveness in Prototyping
Cost-effectiveness is crucial in engineering and product development. Autodesk fluid dynamics solutions help in cutting costs through diminished material waste and the reduction of trial-and-error methodologies in prototyping. Effective fluid simulations enable teams to predict the performance of designs without extensive physical tests.
By utilizing simulations, organizations can identify weaknesses in their design early in the process. Addressing these issues virtually results in fewer physical prototypes, saving both resources and time. Ultimately, this predictive power ensures that when a product does reach the manufacturing stage, it is considerably โready,โ leading to fewer returns or adjustments during the production run.
"The early identification of design flaws reduces the downstream costs associated with prototyping and production errors."
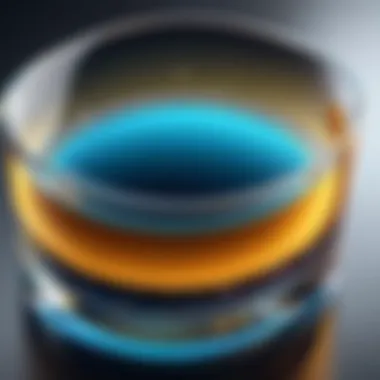
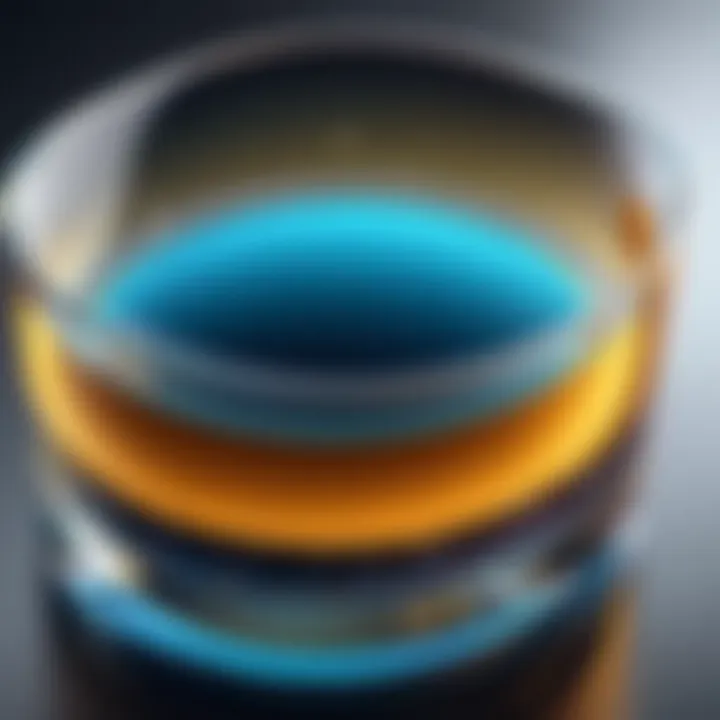
Challenges and Limitations
Understanding the challenges and limitations associated with Autodesk Fluid Dynamics is crucial for professionals and researchers in the field. These factors can significantly impact the performance and outcome of simulations. A clear grasp of these hurdles not only helps in better planning but also enhances the efficiency of fluid dynamics projects.
Computational Demands
Simulating fluid dynamics requires substantial computational resources. The complexity of the calculations often leads to high demands on both hardware and software. The Navier-Stokes equations, which govern fluid motion, can be resource-intensive to solve accurately. Users may need advanced workstations or access to cloud computing services to handle larger and more intricate simulations.
Limited computational power can lead to longer processing times, thus delaying project timelines. Therefore, it is important for users to evaluate their hardware capabilities before embarking on extensive simulations. Many professionals opt for optimization techniques to manage computational demands more effectively. These may include simplifying geometries or using adaptive mesh refinement to strike a balance between accuracy and computational load.
Learning Curve for Users
Adopting Autodesk Fluid Dynamics tools also presents a learning curve for many users. Even those with a background in engineering or IT may find the software's functionalities complex. Familiarization with simulation settings, understanding results, and interpreting fluid behavior require time and practice.
Effective training can mitigate this issue. Online tutorials, documentation, and user forums are valuable resources. However, the initial investment in learning can be a barrier for some. New users might feel overwhelmed or frustrated, which might lead to suboptimal use of the software. Yet, as proficiency grows, users often discover the full potential of the software, leading to better simulation outcomes and project results.
Accuracy vs. Speed Trade-Off
In fluid dynamics simulation, there exists a constant trade-off between accuracy and speed. High fidelity simulations deliver more accurate results but at the expense of increased computational time. Conversely, faster simulations may lead to less accurate predictions, which could compromise project integrity.
Users must determine the acceptable level of accuracy for their specific applications. For example, in preliminary studies, a quicker approximation might suffice, while final design assessments demand precise results. Recognizing when to prioritize speed or accuracy is foundational to effective fluid dynamics management.
Future Trends in Fluid Dynamics Simulation
The realm of fluid dynamics simulation stands at a pivotal juncture, where technology is evolving rapidly. The significance of understanding the future trends in this area is essential for professionals and students to harness capabilities that enhance efficiency and accuracy in their work. The integration of increasingly sophisticated tools not only improves outcomes but also influences methodoly and approach to fluid dynamics. This involves examining various components that drive this progression, including advancements in computational power, the incorporation of artificial intelligence, and the emergence of real-time simulation capabilities.
Advancements in Computational Power
One of the most fundamental elements shaping the future of fluid dynamics simulation is the dramatic advancement in computational power. Modern workstations and cloud computing solutions facilitate simulations once deemed impractical due to resource limitations. As computational power increases, it allows for larger datasets and more complex simulations. Engineers can model intricate systems with greater detail, leading to more accurate predictions.
These advancements also mean that simulations can run more efficiently, reducing the time required for analysis significantly. Multi-core processors and graphical processing units (GPUs) have redefined what's possible in terms of speed and efficiency. Therefore, the ability to tackle expansive models and real-world scenarios is heightened, giving professionals the opportunity to innovate and refine their designs.
Artificial Intelligence Integration
Artificial intelligence is becoming a crucial ally in fluid dynamics simulation. The integration of AI techniques enhances the ability to uncover patterns and optimize outcomes effectively. Machine learning models can evaluate vast amounts of simulation data to discern subtle relationships that human analysis might overlook.
For instance, neural networks can predict the results of fluid behavior in response to various inputs, offering engineers advanced insights. Furthermore, these AI-powered methodologies can automate the analysis process, leading to swift decision-making in design and engineering contexts. This shift towards AI brings about a transformative change, providing the potential to explore design spaces that were previously inaccessible, thereby elevating the outcome quality.
Real-Time Simulation Capabilities
The ability to conduct real-time simulations poses another exciting trend. This capability is crucial in scenarios where immediate feedback is vital, such as in design environments or control systems. Real-time simulation allows users to manipulate models and see the effects of different variables on fluid behavior instantaneously.
With platforms becoming more intuitive, professionals can adjust parameters in real-time, affording a hands-on approach to simulation and design. This leads to increased collaboration among teams and fosters innovative design strategies.
"Real-time capabilities revolutionize how engineers interact with simulations, enhancing both learning and design processes."
Finale
The conclusion of this article emphasizes the significance of Autodesk Fluid Dynamics in contemporary engineering and design practices. This section synthesizes the core concepts discussed and illustrates the profound impact that Autodesk's tools have on fluid simulation. Understanding these differences profoundly affects how professionals approach fluid dynamics, enabling more efficient and effective solutions across various industries.
Recap of Key Points
In summary, the following points have been highlighted throughout the article:
- Defining Fluid Dynamics: This concept serves as the foundation for simulations, shaping how real-world fluid behaviors are modeled.
- Autodeskโs Pioneering Role: Its software, like Autodesk CFD, empowers engineers to conduct complex simulations, refine designs, and predict performance more accurately.
- Core Simulation Concepts: The Navier-Stokes equations, turbulence modeling techniques, and boundary conditions are pivotal for achieving reliable results in fluid dynamics.
- Practical Applications: From aerospace to environmental solutions, Autodesk tools are instrumental in addressing real-world challenges by enhancing design efficiency and accuracy.
- Benefits Over Traditional Solutions: The integration of Autodesk tools in fluid dynamics leads to improved cost-effectiveness, consistent accuracy, and faster iterations in prototyping.
- Challenges and Limitations: Itโs crucial to recognize the computational demands and the learning curve that cal accompany such powerful tools, though these are outweighed by the potential advantages.
- Future Trends: The constant evolution towards real-time simulations and the integration of Artificial Intelligence will further enhance Autodesk Fluid Dynamics applications.
The Future of Autodesk Fluid Dynamics
Looking ahead, Autodesk Fluid Dynamics is on the brink of significant developments. The infusion of advanced computational resources continues to expand the horizons of fluif dynamics simulations. Innovations such as real-time analysis reflect a shift towards more interactive and immediate feedback in design processes. Furthermore, the integration of artificial intelligence holds great promise in automating and refining simulation tasks, allowing users to focus on strategic decision-making rather than manual computations.
The symbiosis of these technologies with existing Autodesk solutions will enhance their robustness. This is crucial in high-stakes industries that rely on precision and speed. As these tools evolve, they will undoubtedly play a significant role in pushing the boundaries of what's possible in fluid dynamics. The continuous improvement approaches suggest that professionals in this field must keep adapting and enhancing their skill sets to remain relevant in this dynamic landscape.
"The goal of Autodesk Fluid Dynamics is not just to simulate the past but to model and predict the future of fluid behavior across various applications."
Therefore, as we look to the future, it is clear that a strategic approach to embracing technology can lead to groundbreaking advancements in fluid dynamics. As professionals familiarize themselves with these advancements, they can harness the full potential of Autodesk's offerings to achieve remarkable outcomes in their respective fields.