Popular MES Systems: An In-Depth Analysis
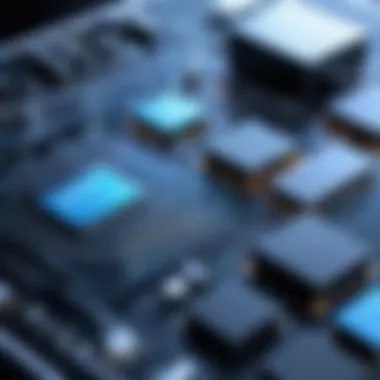
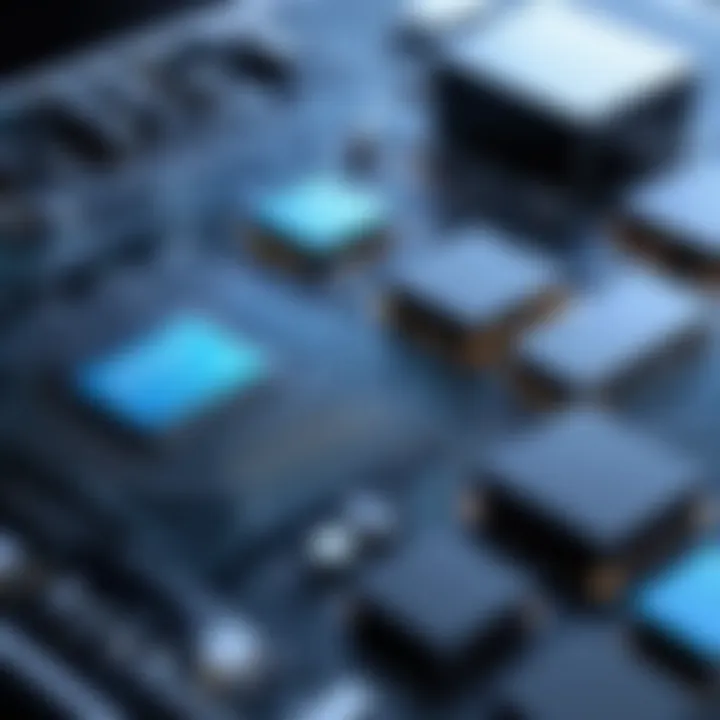
Intro
Manufacturing Execution Systems (MES) play a crucial role in modern manufacturing environments. These systems enhance process efficiency and provide real-time visibility into production operations. As businesses look to optimize their processes, understanding MES becomes essential. This article seeks to offer an in-depth analysis to assist professionals in choosing the right MES for their needs.
A comprehensive overview of popular MES systems will be discussed, addressing their fundamental purposes and functions, key features, key benefits, installation processes, and system requirements. By understanding these aspects, readers will be better positioned to evaluate different systems, helping them to navigate through the complexities of manufacturing technology effectively.
Software Overview
Purpose and Function of the Software
MES software serves as a bridge between enterprise resource planning (ERP) systems and production processes. It enables managers to monitor and control manufacturing operations in real-time. The primary goal is to improve efficiency, enhance product quality, and reduce operational costs. MES software collects data from machines and workers, providing insights that inform decision-making throughout the production cycle.
Key Features and Benefits
Some of the critical features that define MES software include:
- Real-time monitoring of production lines, enabling immediate responses to issues.
- Data collection from various points in the manufacturing process for accurate analytics.
- Production scheduling tools that optimize the workflow and resource allocation.
- Quality management features that track compliance and ensure standards are met.
- Integration options that allow the MES to connect with other systems, like ERP and supply chain management.
The benefits of these features often manifest in the following ways:
- Increased operational efficiency through optimized processes.
- Improved visibility into production, leading to informed decisions.
- Enhanced product quality by minimizing errors and defects.
- Cost savings derived from better resource utilization and reduced downtime.
"A robust MES can be the backbone of modern manufacturing, transforming data into actionable insights."
Installation and Setup
System Requirements
Before considering installation, it is vital to understand the system requirements for various MES solutions. Requirements will typically fall into several categories:
- Hardware: Specific processors, memory, and storage devices are necessary to support the software's functionality.
- Operating System: Compatibility with existing systems, such as Windows or Linux, is a key factor.
- Database Management Systems: Many MES solutions require a robust database system for effective data handling.
Installation Process
The installation of MES software can vary, but a typical process may include the following steps:
- Preparation: Assess hardware and software requirements. Ensure all systems are compliant.
- Installation: Follow the software vendor's guidelines to initiate installation on designated machines.
- Configuration: Configure settings to align with business processes, ensuring the system meets specific requirements.
- Testing: Conduct thorough testing to verify that all features are functioning correctly.
- Training: Provide necessary training to end-users on how to operate the system efficiently.
These steps ensure the smooth integration of MES into the existing organizational framework, setting the stage for enhanced operational performance.
Understanding Manufacturing Execution Systems
Understanding Manufacturing Execution Systems (MES) is crucial for grasping how modern manufacturing operates. With industry increasingly focused on efficiency and precision, MES plays a vital role. It acts as the backbone of production processes, providing real-time insights that drive decision-making. By facilitating the connection between business operations and shop floor activities, MES helps organizations maximize productivity. Manufacturers aiming to streamline operations must consider MES as an essential tool.
Definition of MES
Manufacturing Execution Systems are software solutions that manage and monitor work-in-progress on the factory floor. They provide visibility into production processes by tracking materials, monitoring equipment performance, and capturing data related to work operations. The primary aim of MES is to improve manufacturing efficiency through real-time information. This enables managers to make informed decisions that reduce downtime and enhance overall process flow.
Historical Context
The concept of MES began to emerge during the late 20th century, aligning with the rise of computers in industrial settings. Initially, MES focused on basic production scheduling and data collection. Over time, advancements in technology led to more sophisticated functionalities, integrating with other systems such as Enterprise Resource Planning (ERP). Today, MES plays an integral role in smart manufacturing and Industry 4.0, adapting to new technologies such as IoT (Internet of Things) and automation.
Key Components of MES
The effectiveness of a Manufacturing Execution System hinges on several critical components:
Infrastructure
The infrastructure of an MES involves the hardware and software frameworks that support its operations. This includes servers, databases, and network connectivity. A robust infrastructure is essential for processing large volumes of data in real-time. The key characteristic of a strong MES infrastructure is its scalability, allowing organizations to expand their operations with ease as business needs evolve.
Unique Feature: The ability to integrate with various systems and technologies enhances its value. However, the complexity of the infrastructure can lead to initial setup challenges.
Data Management Tools
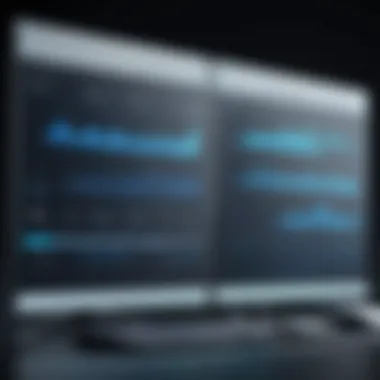
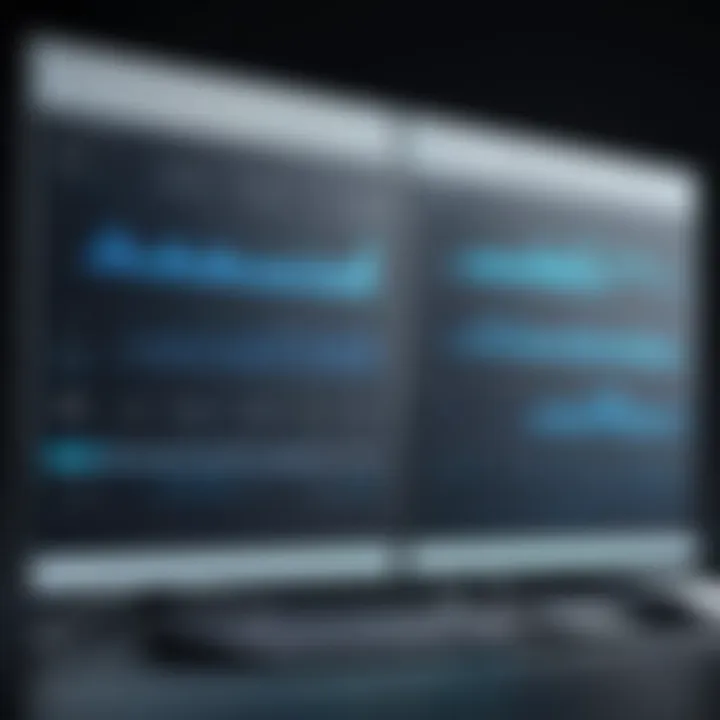
Data management tools in MES enable the capture, storage, and analysis of production data. These tools provide insights into performance metrics, allowing manufacturers to identify areas for improvement. A standout characteristic is the capability to perform real-time analytics on vast datasets.
Unique Feature: The integration of analytics can reveal trends and patterns, aiding in predictive maintenance and process optimization. While powerful, the challenge lies in effectively training staff to utilize these tools.
User Interface
The user interface (UI) is the means through which operators interact with the MES. A well-designed UI streamlines the user experience, making it easy for operators to retrieve crucial information quickly. A key characteristic is intuitiveness, which reduces the learning curve for new users.
Unique Feature: Modern MES systems incorporate visual dashboards that present data in a user-friendly format. Nonetheless, an overly complex UI may hinder usability, impacting overall system effectiveness.
"A successful MES must blend powerful features with usability to meet the dynamic needs of today’s manufacturing environments."
By understanding these components, organizations can better assess how MES aligns with their production goals.
Significance of MES in Modern Manufacturing
The significance of Manufacturing Execution Systems (MES) in contemporary manufacturing cannot be overstated. MES bridges the gap between the enterprise resource planning systems and the production line, allowing organizations to maintain control over their manufacturing processes. Its role is increasingly vital in a landscape marked by heightened competition and rigorous regulatory requirements. An effective MES not only enhances productivity but also assures quality, which are essential for sustaining a business in today’s market.
Real-time Data Monitoring
One of the foremost advantages of MES is its capacity for real-time data monitoring. The ability to track production metrics instantaneously offers managers and operators critical insights into operations. An MES generates data regarding cycle times, equipment utilization, and operational bottlenecks, facilitating quick decision-making. Such immediacy helps in identifying inefficiencies or deviations from the desired outcomes, enabling swift corrective actions. In an environment where time is of the essence, this functionality is indispensable for minimizing downtime and maximizing throughput.
Improvement in Efficiency
Improving operational efficiency is perhaps the most compelling argument for implementing an MES. By automating data collection and providing visibility across the production process, an MES helps streamline workflows. Processes that once required manual input can become automatic, leading to fewer errors and reduced labor costs. With accurate forecasting and resource allocation, businesses can optimize their workflows to better meet production schedules. The result is a more agile manufacturing environment that can swiftly adapt to changing market needs.
Quality Control and Compliance
Quality control is another essential aspect of MES. Maintaining standards in production processes is crucial to ensuring customer satisfaction and adherence to regulatory requirements. An MES enables manufacturers to implement rigorous quality checks at every step. It records deviations and alerts teams in real-time, allowing immediate investigations and remediations. Consequently, compliance with industry regulations becomes more manageable. By documenting processes and outcomes accurately, businesses can easily provide audits and certifications when required.
"Real-time monitoring, efficiency improvements, and stringent quality control are essential elements of modern MES solutions."
In sum, the significance of MES in modern manufacturing resides in its ability to provide essential insights and streamline processes, ensuring that manufacturers can meet today’s demands while planning for future growth. As the manufacturing landscape continues to evolve, the need for such systems will only become more critical.
Market Overview of MES Systems
The market overview of Manufacturing Execution Systems (MES) provides critical insights into the competitive landscape that shapes modern manufacturing. Understanding this sector illuminates key players, pricing strategies, and evolving technology trends. Such knowledge aids businesses in making informed decisions about which MES solutions to adopt, based on their unique needs.
Leading MES Providers
Market share analysis
Analyzing the market share of leading MES providers offers a glimpse into the dominance of certain players. Prominent organizations like Siemens, Rockwell Automation, and Schneider Electric hold significant portions of the market, influencing trends and customer choices. These companies excel in various sectors due to their extensive experience, robust feature sets, and strong support systems.
One key characteristic of market share analysis is the ability to assess how customer loyalty correlates with specific MES provider characteristics. A provider like Siemens, known for its comprehensive suite of features, often leads to higher customer satisfaction and retention rates. This, in turn, solidifies its market position. The advantage here is a stable revenue stream for these companies, enhancing their ability to innovate continuously.
"In a rapidly evolving industry, market share is not just about current sales; it reflects long-term trust and satisfaction.”
Industry impact
The impact of leading MES providers on the industry is profound. Their innovations drive technological advancements in manufacturing processes globally. For example, the incorporation of real-time data analytics by providers such as Rockwell Automation has transformed operational efficiencies in many factories. This enhancement not only improves product quality but also reduces waste, contributing to more sustainable practices.
A unique feature of the industry impact is the feedback loop these providers create; as they introduce new technologies, they stimulate adoption across smaller players and industries. The benefit of this ecosystem is a collective advancement in manufacturing capabilities. However, a potential disadvantage might be the occasional complacency seen with legacy systems, which can hinder market newcomers.
Price Range and Licensing Models
Understanding the price range and licensing models for MES systems is vital for organizations to allocate their budgets effectively. MES providers often employ various pricing strategies, including subscription-based models and one-time licensing fees. The choice between them can influence overall costs; companies must consider factors such as long-term value and the total cost of ownership.
Emerging Trends in MES Technology
Emerging trends in MES technology signal the future direction of this sector. Cloud computing, for example, offers unprecedented flexibility and scalability for MES solutions. Integration with Internet of Things (IoT) devices also provides enhanced data collection capabilities, which optimize operations. Companies looking to implement MES should stay updated on these trends to remain competitive in the evolving landscape.
Emphasing these aspects provides a clear picture of not only the current market but also the foundational elements that will shape its future.
Comparative Analysis of Popular MES Systems
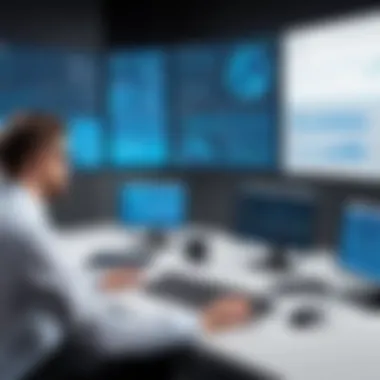
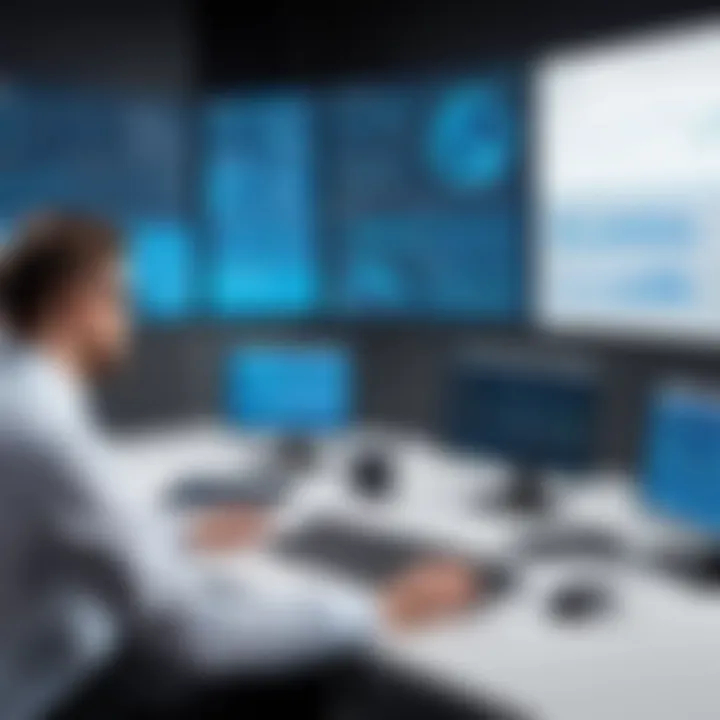
A comparative analysis of popular Manufacturing Execution Systems (MES) is crucial for any organization considering the implementation of such systems. This analysis provides clarity on the available options in the market. MES systems vary significantly in terms of functionalities, features, and overall effectiveness. Understanding these differences helps stakeholders make informed decisions that align with their specific operational needs.
When evaluating various MES solutions, several key factors come into play. These include scalability, ease of integration, real-time data capabilities, and user interface design. Each of these elements contributes to the system’s performance and, ultimately, to the success of the manufacturing processes they support. A thorough comparison also reveals both the advantages and limitations of each system, allowing organizations to weigh pros and cons effectively. This section will detail three popular MES solutions, examining their core functionalities and their strengths and weaknesses.
System A: Overview and Features
Core functionalities
System A is renowned for its comprehensive suite of core functionalities. One significant aspect is its impressive data analytics capabilities. Firms leverage these tools for better decision making and operational efficiency. User-friendly dashboards allow real-time monitoring of production metrics, which enhances responsiveness. Another notable feature is its versatility across various industries, making it a fitting choice for organizations with diverse manufacturing needs.
However, System A's complexity can pose challenges. Organizations must invest in training to utilize all its functionalities effectively.
Pros and cons
The pros of System A include its robust analytics and real-time monitoring features, which are essential for modern manufacturing. Its popularity stems from its flexibility and adaptability to different manufacturing environments. However, it also has cons. The initial setup can be time-consuming and costly. Also, firms might face hurdles if they lack the necessary infrastructure for effective implementation.
System B: Overview and Features
Core functionalities
System B distinguishes itself with excellent integration capabilities. Its core functionalities allow seamless connections with existing ERP and supply chain systems. This characteristic plays a pivotal role in streamlining operations across departments. Users can expect automatic data transfers, which minimize manual input and reduce errors.
Yet, System B shows some limitations. While it integrates well, its overall functionality may lack depth in data analytics compared to competitors.
Pros and cons
Key advantages of System B are its ease of integration and strong support for workflow automation. These features collectively contribute to efficiency, saving time and resources over traditional methods. Conversely, some users find that the lack of advanced analytics tools may hinder deeper insights into production processes. Thus, firms may need to supplement System B with additional systems for comprehensive data analysis.
System C: Overview and Features
Core functionalities
System C is known for its emphasis on user interface and experience. The intuitive design of the user interface supports quick adoption among users, reducing the learning curve. Its core functionalities include mobile access, enabling managers to view production metrics on the go. This flexibility can enhance oversight and timely decision-making.
However, the complete reliance on a user-friendly interface sometimes comes at the cost of depth in functionalities. Users may find certain advanced features lacking compared to other systems.
Pros and cons
System C excels in adaptability with its mobile capabilities and easy-to-use interface. These aspects appeal to businesses where managers need to be mobile and responsive. However, its limitations can also discourage higher-level analytics. Companies seeking detailed reports and more complex functionalities may need additional solutions, leading to a fragmented system architecture.
Implementing an MES System
Implementing a Manufacturing Execution System (MES) is a pivotal step for companies aiming to enhance their operational efficacy. Proper execution of MES systems can lead to significant improvements in production monitoring, quality control, and real-time data management. However, the path to successful implementation requires careful planning, integration with existing systems, and adequate training for users. Each of these elements contributes holistically to maximizing the benefits of MES.
Planning for Implementation
Stakeholder analysis
Stakeholder analysis identifies individuals and groups impacted by the MES implementation. It is crucial to gauge their needs and concerns to ensure successful adoption. Engaging stakeholders from the outset creates a sense of ownership and mitigates resistance later on. This process requires application of techniques like surveys, interviews, and workshops to gather insights. Involving key players promotes transparency and can lead to valuable feedback which may enhance system design. Not only does this encourage collaboration, but it also strengthens the foundation for project acceptance.
Defining objectives
Defining clear objectives is another critical aspect of the planning process. Objectives provide direction for the MES implementation. They serve as benchmarks for measuring success. Establishing specific, measurable, achievable, relevant, and time-bound (SMART) goals ensures clarity in expectations. This focus aligns stakeholders and resources towards common aims. However, poor objective-setting can lead to misaligned efforts, creating gaps between expectations and results. Therefore, precise objective definition is vital for project alignment and effective tracking of progress.
Integration with Existing Systems
Data migration
Data migration involves transferring data from legacy systems to the new MES. This task is essential as it ensures continuity and utilization of existing information. A well-structured data migration strategy minimizes downtime and retains historical data integrity. However, care must be taken to handle data discrepancies and ensure compatibility. Thorough testing before and after migration is advisable to safeguard against potential disruptions in operations.
API considerations
API considerations focus on how the MES interfaces with other software systems. A flexible and well-documented API is critical for enabling seamless integration. It allows for communication between new and legacy systems, improving overall operational workflows. Interfacing via APIs can also facilitate automation, reducing manual data entry. Nonetheless, reliance on APIs requires ongoing maintenance and potential troubleshooting. Proper planning in this area will help mitigate integration challenges.
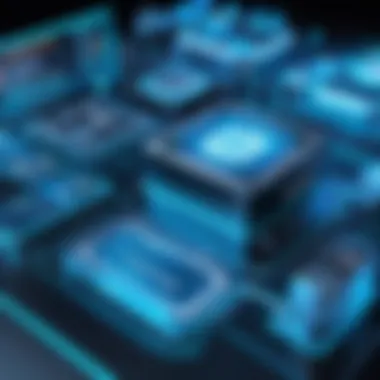
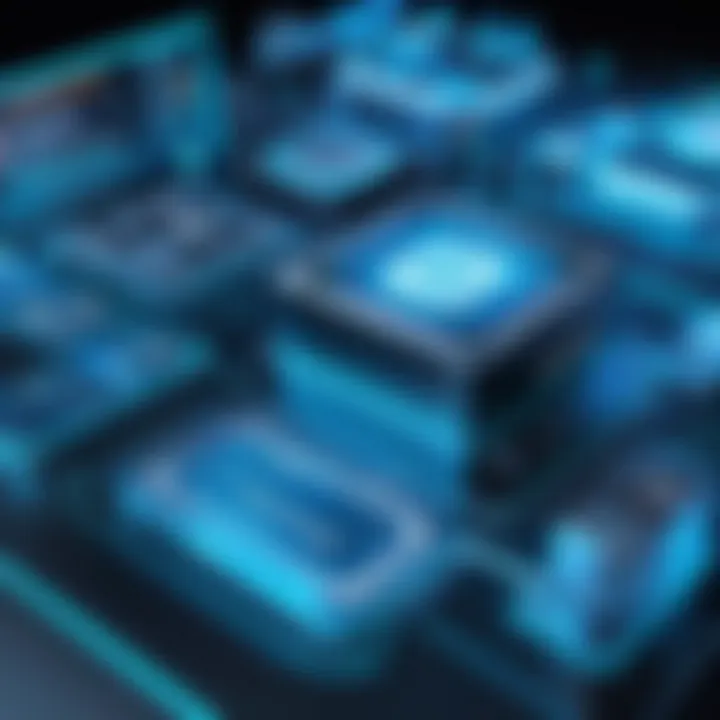
Training and Support
Effective training and support are vital for ensuring that users can maximize the capabilities of the MES system. Comprehensive training programs should be tailored to various user roles, addressing specific functionalities relevant to their tasks. Providing adequate resources and ongoing support enables users to become proficient in using the system. This investment in human capital fosters broader acceptance of MES tools, thereby enhancing operational efficiency. Inadequate training, conversely, can lead to frustration and inefficiencies in production processes.
Implementing MES systems is no small feat, but with careful planning, integration, and training, organizations can harness the full potential of their investment. As these systems evolve, staying informed and prepared for challenges will further ensure continuous improvement.
Challenges in MES Implementation
Implementing a Manufacturing Execution System (MES) is not without its hurdles. The intricacies of any MES initiative can shape its eventual success or failure. By understanding the challenges involved, organizations can better prepare for the obstacles that may arise during implementation. In this section, we will discuss three main challenges: technical challenges, cultural resistance, and budget constraints.
Technical Challenges
Technical challenges are often the most visible barriers in MES implementation. These can include compatibility issues with existing systems, data integrity problems, and challenges related to system configuration. For instance, integrating an MES with legacy equipment may require custom development work to ensure smooth data exchange.
Adopting an MES often means dealing with significant volumes of data. The complexity of managing vast datasets raises concerns about data accuracy and automation. Data migration is another aspect that can delay implementation. Ensuring that historical data is transferred correctly while maintaining relevance and accuracy can be daunting.
Additionally, system configuration demands careful attention. An MES must be tailored to fit specific business processes. Poor configuration can lead to misalignment with operational goals, thus diminishing the system's effectiveness. The ongoing support for the technical infrastructure must not be overlooked either, as maintenance is essential for long-term performance.
Cultural Resistance
Cultural resistance is a subtle yet significant challenge during MES implementation. Employees often resist changes to their established workflows, especially when they perceive these changes as a threat to their job security or professional practice. A lack of understanding of the benefits an MES brings can lead to skepticism and reluctance to adapt.
For a successful MES implementation, it is crucial to foster a culture of collaboration and continuous improvement. Educating the workforce about how MES can enhance their roles can mitigate resistance. Engaging impacted employees early in the process can also promote buy-in and reduce friction.
Key tactics to address cultural resistance include:
- Transparent communication about the goals of MES implementation
- Training sessions to improve familiarity with the new system
- Involving key team members in planning and decision-making processes
These steps can cultivate a more welcoming environment for technological advancements, resulting in higher adoption rates of the MES.
Budget Constraints
Budget constraints are a common hurdle in MES implementation. The initial investment required to implement the system can be significant, encompassing software licensing, hardware upgrades, and employee training. Many organizations have limited financial resources, which can restrict their abilities to fully adopt MES or maintain ongoing support.
Cost management is paramount. Successful implementation often relies on a phased approach, allowing companies to distribute costs over time. Furthermore, organizations should consider the long-term return on investment, as a well-integrated MES can lead to enhanced productivity and reduced operational costs over time.
Factors that can contribute to budget overruns include:
- Underestimating the complexity of integration with current systems
- Unexpected technical problems during deployment
- Inadequate training that leads to inefficient usage of the system
Future of MES Systems
The future of Manufacturing Execution Systems (MES) is increasingly relevant in the context of modern manufacturing due to rapid technological advancements. MES systems are evolving from basic data collection tools to integral components that drive operational efficiencies, optimize quality, and enhance decision-making. Professionals in industrial technology must consider several key elements shaping the MES landscape in the coming years.
Firstly, integratation with newer technologies will be vital. As organizations strive to achieve higher efficiency, the synergy between MES and emerging technologies will become essential. This integration is no longer an option but a necessity to remain competitive.
Secondly, data analytics and real-time reporting will continue to gain importance. With big data becoming more prevalent, the MES of the future must be capable of harnessing vast amounts of data to produce actionable insights. This aligns with the increasing need for responsiveness in manufacturing operations — a shift toward data-driven decision making.
Thirdly, organizations must consider user-centric design. Adoption rates often hinge on the usability of MES interfaces. Future systems should prioritize intuitive user experiences, enabling even non-technical users to interact effectively with the software. Streamlined and flexible interfaces can enhance employee engagement and proficiency.
Impact of IoT and Industry 4.
The Internet of Things (IoT) and Industry 4.0 represent a significant turning point for manufacturing execution systems. The integration of connected devices and smart machinery enhances real-time data collection and analysis. As machines become interconnected, MES must adapt to incorporate vast amounts of data flowing from these sources.
Through IoT, MES systems will enable better visibility of operations. Sensors can track machine performance and product quality continuously, allowing for immediate corrective actions when necessary. This level of monitoring is essential for achieving high standards of operational excellence and compliance.
Furthermore, the data coming from IoT devices allows for predictive maintenance. Instead of relying on a schedule, MES can analyze performance data to forecast when a machine will likely fail, thus preventing costly downtime. This shift transforms maintenance from being reactive to proactive.
However, challenges exist in the foreach of IoT integration. Concerns about data security and the need for standardized communication protocols require careful consideration. Companies should plan their implementation strategies to mitigate these risks while enjoying the benefits of IoT.
Artificial Intelligence in MES
Artificial Intelligence (AI) is revolutionizing the capabilities of Manufacturing Execution Systems. The potential of AI lies in its ability to process large data sets rapidly and with precision. This capacity allows MES to transition from merely reporting data to providing predictive insights that can inform operational strategies.
One significant application of AI in MES is through advanced analytics. By employing machine learning algorithms, MES can identify patterns in production data, enabling manufacturers to adapt operations based on real-time insights. This kind of flexibility is critical in maintaining competitiveness in today’s fast-paced market.
Additionally, AI can facilitate automated decision-making processes. For instance, AI-powered systems can optimize production schedules by analyzing various parameters, such as equipment availability and workforce capacity. This reduces lead times and enhances overall plant productivity.
Despite these advancements, companies must address a few obstacles to adopt AI successfully. Data quality, an effective training of AI models, and integration into existing workflows are issues that require thorough planning and investment.
In summary, the incorporation of AI presents immense opportunities for MES systems. The future holds not only enhanced operational efficiencies but also a strategic advantage for those who can capitalize on the evolving landscape of technology.