Understanding QMS Siemens: An In-Depth Exploration
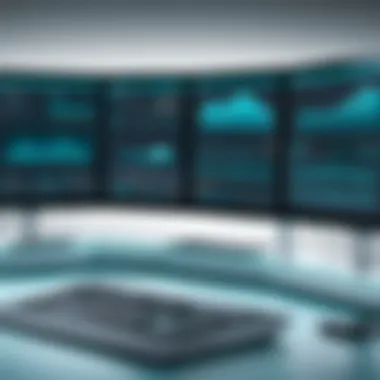
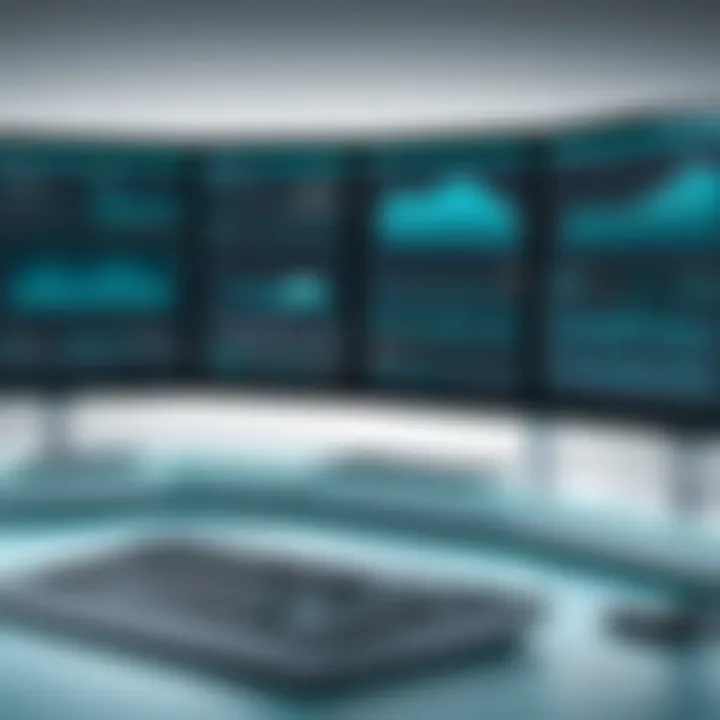
Intro
In today’s competitive environment, organizations seek methods to improve quality and efficiency. One important tool available to enterprises is the Quality Management System (QMS) by Siemens. This comprehensive platform provides a structured approach to help manage quality processes effectively. In this article, we will explore various aspects of Siemens' QMS, including its purpose, functionality, installation requirements, and features that stand out in the industry.
Software Overview
The QMS from Siemens serves as an integral solution for organizations looking to streamline their quality assurance processes. Its core functionality revolves around ensuring that production and operational processes meet regulatory standards and customer expectations.
Purpose and function of the software
The primary purpose of Siemens' QMS is to enhance operational efficiency by providing systematic control over processes. The software manages quality-related data, enables compliance tracking, and helps organizations maintain high standards.
Key features and benefits
Siemens' QMS boasts several notable features:
- Centralized Management: It allows users to maintain all quality data in one platform, fostering easy access and reporting.
- Automation Capabilities: Routine tasks and processes are automated, reducing human error and saving time.
- Integration Options: The system can be integrated with other enterprise applications, allowing seamless data exchange.
- Strong Reporting Tools: Users can generate comprehensive reports, which aid in decision-making and compliance assessments.
The benefits of implementing Siemens' QMS are substantial. It helps improve product quality, boosts customer satisfaction, and reduces business risks associated with non-compliance. These elements contribute to a more robust operational framework.
Installation and Setup
Setting up Siemens’ QMS requires attention to detail. Understanding system requirements is crucial for smooth installation.
System requirements
Before installing the software, organizations should ensure they have the necessary hardware and software infrastructure:
- Operating System: Compatible with Windows Server versions.
- Database: Must support SQL Server or Oracle for data management.
- Memory and Storage: Adequate RAM (minimum 8GB) and storage space depending on data volume.
Installation process
The installation process for Siemens' QMS involves several steps:
- Download the installation package from the Siemens website.
- Run the setup file. Follow prompts for accepting terms and conditions.
- Specify installation directory. Ensure enough space is available.
- Select additional options. Choose any components or tools to include with the installation.
- Complete the setup. Verify installation status and perform initial system checks.
Completing these steps successfully ensures that the QMS is ready for configuration according to organizational needs.
The End
Siemens’ QMS offers a structured approach to quality management, aligning with industry standards. Understanding its key features, installation requirements, and benefits can significantly enhance operational efficiency. Implementing such a system can lead to greater compliance and ultimately foster a culture of continuous improvement.
Prologue to QMS Siemens
Quality Management Systems (QMS) have become essential for organizations aiming to enhance their operational efficiency and ensure compliance with industry standards. Understanding QMS Siemens is particularly relevant as Siemens represents a fusion of technology and innovation. Their approach to quality management is informative for various sectors, including manufacturing and healthcare. The ability to optimize processes while maintaining high-quality output sets Siemens apart.
In the current business landscape, which is highly competitive and regulated, organizations must adopt robust quality management systems. Siemens offers a comprehensive QMS solution that integrates with their array of products. This enables organizations to streamline their operations and reduce the risk of errors. The effective use of technological tools within the QMS is key to meeting stringent regulatory requirements.
Moreover, the significance of a QMS extends beyond just meeting compliance. It serves as a framework for continuous improvement, aligning operational practices with strategic business goals. Adopting QMS Siemens can lead to lower costs and better customer satisfaction. The following sections will delve deeper into the fundamentals of QMS, its core components, and the distinctive role that Siemens plays in it.
Defining Quality Management Systems
Quality Management Systems are structured frameworks aimed at ensuring the consistent delivery of quality products and services. These systems involve policies, processes, and procedures that govern how quality assurance is integrated and maintained across an organization.
- Key Elements: A QMS typically includes elements such as quality planning, quality control, quality assurance, and quality improvement.
- Benefits: By implementing these systems, organizations can achieve higher efficiency and reduce waste.
- Standards: Various standards, like ISO 9001, provide guidance for establishing a QMS.
The successful deployment of a QMS hinges on effective leadership, clear communication, and a culture of quality. In essence, a well-defined QMS is pivotal to driving business success.
Overview of Siemens as a Technology Leader
Siemens is recognized globally as a technology leader known for its contributions to various sectors, including automation, digitalization, and smart infrastructure. With a strong emphasis on innovation, Siemens has established itself as a pioneer in integrating quality management into its product offerings.
- Innovation Focus: Siemens invests heavily in research and development to stay ahead in technology trends. This commitment ensures that their QMS integrates seamlessly with other technologies.
- Industry Applications: The company's solutions are applicable across several industries, such as manufacturing, energy, and healthcare.
Siemens' position as a technology leader not only enriches its product capabilities but also places them at the forefront of modern quality management practices. The integration of technology within the QMS highlights Siemens' role as a facilitator for operational excellence.
Core Components of QMS Siemens
The core components of QMS Siemens play a crucial role in ensuring the system's functionality and effectiveness. These components are structured to facilitate compliance, enhance efficiency, and manage quality across various processes. Understanding these elements allows organizations to leverage the full potential of Siemens’ Quality Management System to meet their operational goals effectively. Each component contributes to a holistic approach to quality management, enabling the organization to streamline processes, maintain documentation, manage changes, and uphold standards.
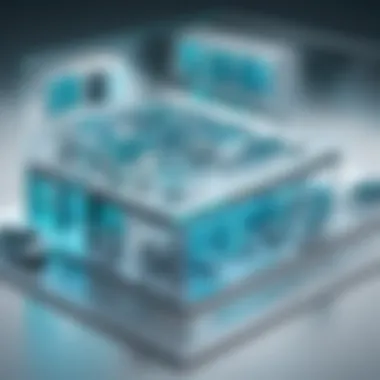
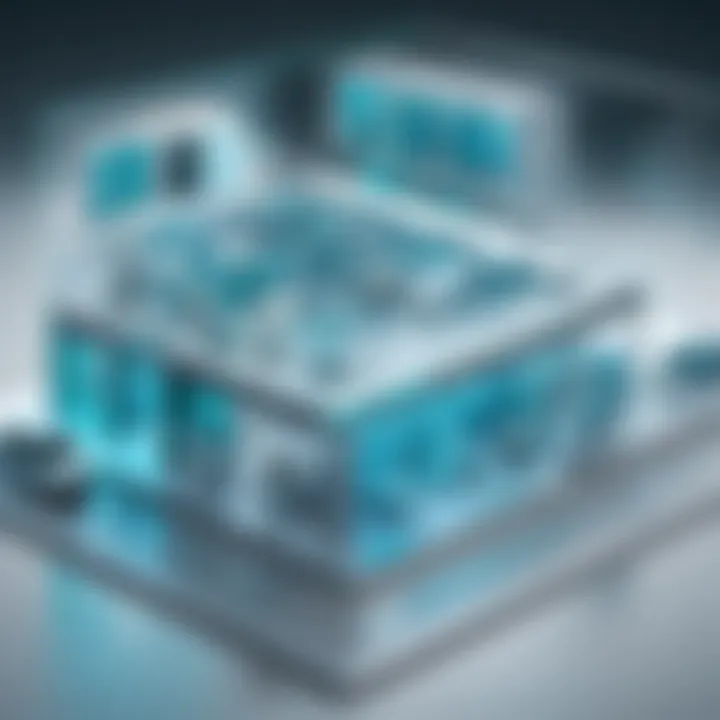
Document Control and Management
Document control is a fundamental aspect of any Quality Management System, and Siemens' QMS excels in this area. This component ensures that all quality-related documents are properly managed throughout their lifecycle. Implementation of strict version control helps in tracking changes, maintaining document integrity, and preventing the use of outdated information.
The ease of document retrieval also minimizes delays in accessing critical information. Having a structured process for documenting protocols, procedures, and evidence is paramount for demonstrating compliance. In large organizations, where multiple teams operate simultaneously, the ability to centralize documents becomes even more vital. Proper document control supports transparency and accountability, thus reinforcing the quality culture within organizations.
Audit Management Features
Audits in quality management serve as a systematic review of processes and compliance statuses. Siemens' QMS provides robust audit management features that facilitate planning, execution, and tracking of audit activities. With the integrated audit tools, organizations can schedule audits, assign responsibilities, and ensure timely follow-ups on findings.
Automated notifications can prompt relevant personnel, ensuring that no audit is overlooked. Moreover, generating comprehensive reports aids in assessing compliance with internal policies and external regulations. Continuous auditing helps in identifying areas that require improvement, ensuring that the quality systems remain effective and can evolve in response to emerging challenges.
Non-Conformance Management
Non-conformance management is essential for identifying and rectifying deviations from set quality standards. In the context of Siemens’ QMS, this component provides a structured process to report, investigate, and resolve non-conformances. Efficiently managing non-conformances helps to prevent recurrence by addressing root causes and formulating corrective actions.
The system allows documentation of the non-conformance incidents, fostering a culture of learning rather than punishment, which is beneficial for employee morale and trust. Additionally, tracking non-conformances over time can reveal patterns, enabling organizations to implement preventive measures more effectively.
Change Control Processes
Change control is a critical component in ensuring that modifications to processes, products, or systems do not adversely affect quality. Siemens’ QMS has a well-defined change control process that guides organizations through evaluating, approving, and documenting changes. This approach ensures that changes are made systematically, considering the potential impact on quality and compliance.
The system provides tools for assessing risks associated with changes, allowing teams to make informed decisions. Documenting each stage of the change process enhances accountability and traceability. Additionally, ensuring that all stakeholders are informed and adequately trained on new processes helps to minimize disruption to operations.
In summary, the core components of QMS Siemens are designed to provide a comprehensive framework for managing quality. Each element is interconnected, contributing to a more efficient and compliant organization. By adopting these components, companies can achieve better quality outcomes, ultimately leading to enhanced operational excellence.
Functionalities of QMS Siemens
The functionality of QMS Siemens is fundamental in shaping an effective quality management environment. It enables organizations to align their quality processes with both business objectives and industry standards. These functionalities enhance productivity, streamline operations, and foster an atmosphere of continuous improvement. In this section, we will examine three significant functionalities: integration with other Siemens products, real-time data analysis and reporting, and user-friendly interfaces and navigation.
Integration with Other Siemens Products
Integration is one of the strong points of QMS Siemens. The system is designed to work seamlessly with other Siemens software solutions. This interconnectedness leads to enhanced efficiency by allowing users to share data across platforms without significant barriers. Here are some benefits of this integration:
- Unified Data Management: Integration ensures that all relevant data is accessible from a single platform, reducing discrepancies and errors.
- Enhanced Decision-Making: Real-time data sharing aids managers in making informed decisions based on accurate and updated information.
- Streamlined Processes: Tasks that involve multiple software solutions can be managed more effectively, leading to shorter response times.
Furthermore, organizations can customize the integration according to their specific needs, which makes the system scalable and adaptable.
Real-Time Data Analysis and Reporting
Another vital functionality of QMS Siemens is its capability for real-time data analysis and reporting. Organizations today increasingly rely on data-driven insights for operational excellence. The advantages of this functionality include:
- Immediate Insights: The ability to analyze data in real-time allows teams to identify trends and issues swiftly.
- Automated Reporting: Manual reporting consumes time and resources. QMS Siemens automates this process, generating reports instantly and eliminating the chance of human error.
- Customizable Dashboards: Users can create dashboards that display the most relevant metrics. This makes monitoring progress straightforward and effective.
Effective data reporting also plays a role in maintaining compliance with industry standards, as it provides a clear audit trail.
User-Friendly Interfaces and Navigation
User experience is pivotal in any software application, and QMS Siemens excels in this area. Its user-friendly interfaces and navigation features ensure that both novice and experienced users can utilize the system effectively. Key points include:
- Intuitive Design: The interface is intuitive, which cuts down the learning curve for new users. This is particularly beneficial for organizations implementing the system for the first time.
- Easy Navigation: User-friendly navigation helps users to access various functionalities without confusion. Thus, users can focus on quality management tasks rather than figuring out the software.
- Training Support: Although the interface is easy to use, Siemens provides ample training resources. These support mechanisms ensure users feel confident in their ability to operate the system.
"A system's usability can significantly impact user adoption and operational efficiency."
Implementation of QMS Siemens
Implementation of QMS Siemens is a critical phase that can determine the overall success of a quality management initiative. This task demands careful planning, robust training, and ongoing evaluation to ensure that the system aligns with the organization's goals. The benefits of effectively implementing QMS are significant. Organizations can achieve enhanced operational efficiency, improved compliance, and a structured approach to continuous improvement. However, challenges may appear during this process, making it vital to understand key elements involved in the implementation.
Planning for QMS Deployment
Proper planning is the cornerstone of a successful QMS deployment. Organizations must evaluate their current quality management practices before adopting Siemens' system. This involves understanding existing workflows and identifying areas requiring improvement. Effective planning should consider the following aspects:
- Stakeholder Involvement: Engaging team members from various departments can provide valuable insights into existing processes.
- Resource Allocation: It's important to allocate budget and personnel to support the deployment phase, as adequate resources often lead to better implementation outcomes.
- Timeline Development: Establishing a realistic timeline helps manage expectations and ensures that all involved are aware of project milestones.
By addressing these factors, organizations set a solid foundation for a productive deployment process.
Training and Support Mechanisms
Training is essential for ensuring that all users understand how to use the QMS effectively. Siemens offers tailored training programs, which address the needs of various user groups, such as IT personnel, quality managers, and operational staff. Some key features of the training and support mechanisms include:
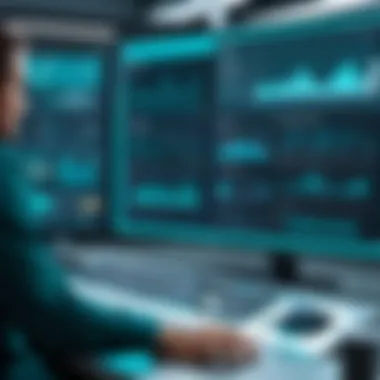
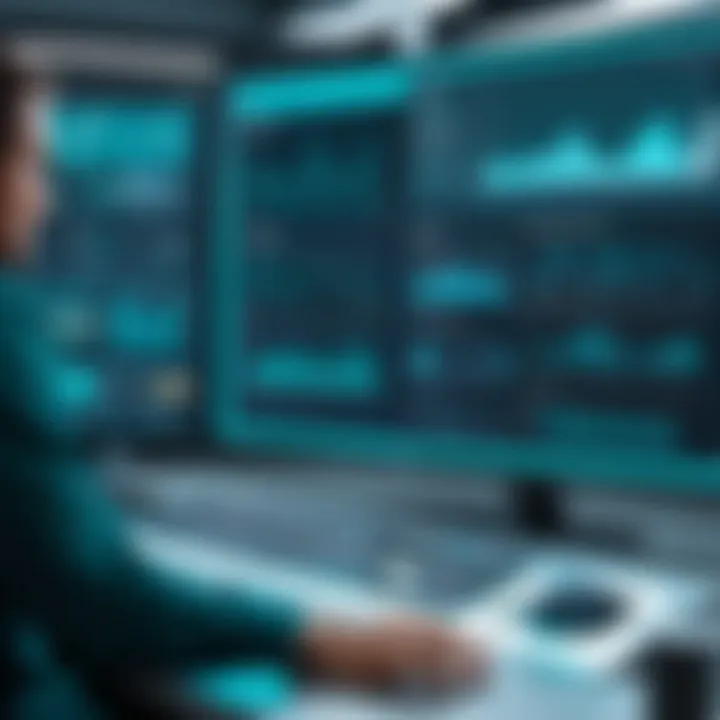
- User-Centric Training Modules: These modules focus on different roles within the organization, catering to specific needs and expertise levels.
- Onboarding Resources: Easily accessible materials and resources help new users acclimatize to the system quickly.
- Continuous Support: A dedicated support team ensures that users receive assistance even post-implementation, helping to resolve queries or technical issues.
This comprehensive training approach fosters a deeper understanding of the system, which is vital for effective utilization.
Measuring Success Post-Implementation
After implementation is complete, evaluating its effectiveness is crucial. Measuring success helps organizations identify strengths and weaknesses in the QMS. Key performance indicators (KPIs) can provide insights into aspects like:
- Process Efficiency: Quantifying time savings or reductions in error rates gives a clear picture of operational improvements.
- Compliance Rates: Assessing adherence to industry standards and regulations ensures that the organization remains compliant.
- User Satisfaction: Gathering feedback from users helps identify areas needing improvement, ensuring ongoing engagement with the system.
"Continuous evaluation is key. If improvements are not measured, they may go unnoticed."
By employing these metrics, organizations can fine-tune their use of QMS Siemens, ultimately cementing its value in fostering a culture of quality.
Benefits of Using QMS Siemens
The adoption of a Quality Management System provided by Siemens brings several advantages that can transform organizational procedures. These benefits encompass operational efficiency, compliance adherence, and pathways for continuous improvement. Organizations that manage to integrate Siemens’ QMS effectively will notice likely enhancements in various functional areas. Understanding these benefits is essential for professionals looking to leverage QMS Siemens for maximized performance.
Enhancing Operational Efficiency
Operational efficiency represents a significant goal for any modern organization. QMS Siemens achieves this by streamlining processes and reducing redundancies. The system includes automation tools that minimize manual tasks and errors, thereby allowing teams to focus on strategic initiatives rather than routine operations.
Some ways QMS Siemens supports operational efficiency include:
- Process Automation: Routine tasks are handled automatically, resulting in time savings.
- Real-Time Monitoring: Supervisors can track process performance instantly, leading to immediate corrections when needed.
- Centralized Data Management: All operational data is stored in one place, enhancing accessibility and decision-making.
The effect of heightened operational efficiency shows directly in resource utilization and cost reductions.
Improving Compliance and Standards Adherence
Compliance with regulatory standards is non-negotiable in industries such as healthcare, manufacturing, and automotive. QMS Siemens helps organizations maintain stringent compliance through its customizable features that align with various regulatory frameworks.
Key points on compliance include:
- Automated Documentation: QMS Siemens facilitates the creation and management of necessary documentation. This ensures every compliance document is up-to-date and easy to retrieve when required.
- Audit Trails: Detailed audit trails are maintained, allowing for easy verification of compliance with standards over time.
- Regular Compliance Assessments: The ability to conduct regular checks to address non-compliance proactively prevents potential fines and damage to reputation.
Maintaining compliance not only safeguards against regulatory issues but also builds trust among customers and stakeholders.
Facilitating Continuous Improvement
Continuous improvement is critical for remaining competitive in any sector. QMS Siemens incorporates tools and methodologies that promote ongoing enhancement of processes and products. This can lead to better performance outcomes and overall satisfaction.
Efficacious continuous improvement strategies provided by QMS Siemens comprise:
- Data-Driven Insights: The system offers analytics and reporting functionalities that help identify areas for improvement based on actual performance data.
- Feedback Loops: The integration of feedback from all stakeholders leads to iterative improvements in processes.
- Kaizen Approach: It supports a culture of continuous, small changes, thus facilitating the integration of gradual improvements.
The capacity to adapt and improve continuously allows organizations to stay ahead of the competition, which is paramount in fast-changing industries.
Real-World Applications
Understanding the practical implications of Quality Management Systems (QMS) is crucial for organizations seeking to optimize their operations. This section examines the real-world applications of QMS Siemens across various industries, highlighting how its tailored solutions enhance operational effectiveness and maintain standards of quality.
Incorporating QMS Siemens into a business can yield significant benefits, including the ability to streamline processes, harness real-time data, and foster a culture of continuous improvement. Each industry presents unique challenges and needs, so it is imperative to explore how QMS Siemens adapts to these requirements.
Case Study: Manufacturing Sector
The manufacturing sector faces distinct challenges related to quality control, production efficiency, and compliance with regulatory standards. Implementing QMS Siemens in this context helps organizations monitor their processes rigorously. This systematic approach reduces waste and inconsistencies while promoting adherence to safety protocols.
One example can be seen in a large manufacturing firm that integrated QMS Siemens into its production line. By employing robust audit management and change control processes, the company effectively minimized defects and enhanced product traceability. The system provided clear documentation methods, which proved invaluable during audits, ensuring compliance with industry regulations.
As a result, this organization not only improved its operational efficiency but also bolstered its reputation in the market.
Case Study: Healthcare Industry
The healthcare sector prioritizes patient safety and stringent regulatory compliance. Here, QMS Siemens has transformative potential. By implementing rigorous non-conformance and document control systems, healthcare organizations can both mitigate risks and promote best practices.
A healthcare facility utilized QMS Siemens to refine its incident reporting and corrective action processes. This resulted in faster response times to patient safety issues. Tracking any non-conformance through detailed documentation led to actionable insights, enhancing overall service quality. For hospitals, the ability to provide consistent patient care while complying with health regulations is critical.
Through these advancements, patient outcomes improved significantly, showcasing the substantial impact that QMS Siemens can have in a highly regulated environment.
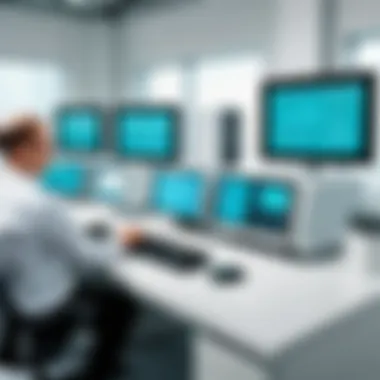
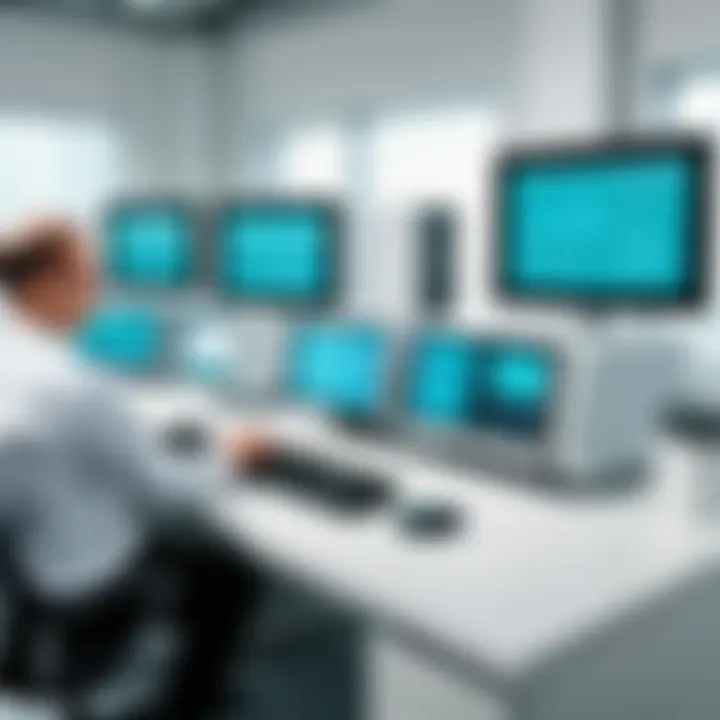
Case Study: Automotive Sector
The automotive industry is known for its emphasis on quality and efficiency, with numerous stakeholders involved in the production chain. QMS Siemens plays a crucial role here by facilitating clear communication and rigorous standards.
An automotive manufacturer adopted QMS Siemens to address the complexities in its supply chain. The system's integration capabilities allowed for smooth collaboration between various departments, from procurement to assembly. This ensured that quality checks were enforced consistently at each stage of production.
Furthermore, with real-time data analysis, management could quickly identify bottlenecks and respond effectively. The outcome was a more agile manufacturing process that reduced lead times and enhanced product reliability.
In sum, these case studies demonstrate the extensive applicability and benefits of QMS Siemens. Each industry can leverage the system to meet its specific needs, thereby achieving significant improvements in quality assurance and operational excellence.
Challenges Faced
In any implementation of a Quality Management System, several challenges can arise that hinder success. Understanding these challenges is crucial for organizations looking to adopt QMS Siemens effectively. The factors detailed below not only highlight obstacles but also outline the importance of addressing them proactively.
Common Implementation Pitfalls
Implementing QMS Siemens can be complex, and organizations often encounter common pitfalls. These include incomplete planning and lack of stakeholder engagement. If the planning phase does not consider all aspects of the system, including resources, technology, and training, the implementation may falter. Moreover, insufficient involvement from key stakeholders can lead to a lack of buy-in, which is essential for successful adoption.
- Inadequate Training: Often, organizations underestimate the importance of training employees. Without proper training, staff may struggle to adapt to the new system, causing frustration and inefficiencies.
- Ignoring User Feedback: Continuous improvement relies on user feedback. Organizations that overlook this aspect may miss critical insights that can enhance the system's functionality.
Managing Resistance to Change
Change can be unsettling. Resistance is a natural human reaction, which is prominent during the implementation of QMS Siemens. Some employees may feel threatened by new processes, fearing that their roles will be affected. It is essential to manage this resistance by fostering an environment of trust and communication.
- Open Communication Channels: Keeping lines of communication open can make a significant difference. When employees understand the benefits and objectives of the QMS, it fosters greater acceptance.
- Involvement in the Process: Engaging employees in the implementation process can provide them with a sense of ownership. This can mitigate fears and create advocates for the new system.
Maintaining System Integrity Over Time
Once QMS Siemens is in place, maintaining its integrity becomes vital. Systems can deteriorate if not regularly monitored and updated. Organizations must establish a culture of continuous quality improvement to uphold system integrity.
- Regular Audits: Conducting regular audits ensures that the system is functioning as intended. This helps identify areas of improvement and adhere to compliance standards effectively.
- Ongoing Training and Support: Continuous training initiatives support users in adapting to updates and changes. Regular training helps reinforce the skills necessary for effective system usage.
Ensuring system integrity requires diligence and commitment from all levels of the organization. Without sustained efforts, even the best quality management systems can fail over time.
Future of QMS Siemens
The importance of addressing the future of QMS Siemens lies in understanding how the system will evolve in response to ongoing challenges and opportunities within industries. As businesses become increasingly complex, the demand for advanced quality management systems rises. Siemens is poised to lead this transformation with innovations that enhance operational capabilities, ensure compliance, and foster quality assurance.
Trends in Quality Management Systems
Quality management systems have undergone significant transformation, driven by several trends that align with technological advancements and market demands. Some of the notable trends include:
- Increased Automation: Automation is at the forefront of modern QMS. By automating documentation, audit trails, and compliance processes, organizations save time and reduce human errors.
- Cloud Computing: The shift to cloud-based platforms brings flexibility and accessibility. This allows teams to access quality management processes remotely, which is particularly beneficial in today's globalized work environment.
- Data-Driven Decision Making: Utilizing data analytics and real-time reporting has become essential. Organizations can identify trends, assess risks, and make informed decisions to improve quality outcomes.
- Integration with Other Systems: The ability to integrate QMS with ERP and CRM systems enhances coordination across departments. This leads to a more comprehensive view of quality management within an organization.
These trends emphasize the need for adaptability and continuous improvement to meet emerging business demands and regulatory requirements.
Emerging Technologies and Their Impact
Emerging technologies are reshaping the landscape of quality management systems. These advancements enable more efficient processes and improved outcomes. Key technologies impacting QMS include:
- Artificial Intelligence (AI): AI is used to analyze historical data and predict quality issues before they occur. This proactive approach mitigates risks and enhances product quality.
- Internet of Things (IoT): IoT devices provide real-time data from manufacturing processes. This data allows for immediate quality assessment and control, driving better decisions and faster responses.
- Blockchain: The transparency and traceability offered by blockchain can enhance trust in quality data. This is especially relevant in industries such as healthcare and food production, where quality assurance is critical.
- Augmented Reality (AR): AR can assist in training and operational processes by providing visual guides and interactive simulations for quality management practices.
These technologies not only bring efficiency but also foster a culture of innovation within organizations, aligning with Siemens’ vision for the future of quality management.
In summary, the future of QMS Siemens is characterized by adaptability to trends and integration of emerging technologies, ultimately propelling organizations towards attaining higher standards of quality and performance.
The continued investment in these areas will ensure that Siemens remains a leader in the quality management landscape.
Closure
The conclusion section serves as a critical component of this article, bringing together the various threads of discussion surrounding Siemens' Quality Management System (QMS). The importance of this conclusion lies in summarizing the extensive insights gained throughout the exploration of QMS. Overall, it not only reinforces the key elements discussed but also prepares the reader for practical applications and future considerations.
Recapping Key Insights
In the previous sections, we examined several pivotal aspects of QMS Siemens. The primary insights include:
- Core Components: Each component, such as document control, audit management, and non-conformance handling plays a crucial role in maintaining a systematic quality approach.
- Functionalities: The system's ability to integrate smoothly with other Siemens products and provide real-time data reporting enhances its usability across different sectors.
- Implementation Challenges: Understanding the common pitfalls and resistance to change helps organizations plan better when adopting QMS.
These insights outline how QMS Siemens not only ensures compliance with quality standards but also supports continuous improvement within various industries.
Final Thoughts on QMS Siemens
QMS Siemens represents a strategic asset for organizations seeking to elevate their quality management efforts. Its robust framework encourages a culture of quality while adapting to the dynamic nature of modern industry demands. Importantly, companies must recognize that implementation is an ongoing process that requires commitment, training, and evaluation.
Moreover, as new technologies emerge, the features of QMS Siemens will likely evolve. Staying updated on these trends is vital for maximizing the system's capabilities. Organizations must not only utilize the current functionalities but also adapt to upcoming advancements to maintain a competitive edge.